Let’s say you own a top-of-the-line sports car. Sleek in appearance, it also has the latest technology under the hood to deliver the performance you seek when you press the accelerator.
Consider what would happen if you decided to install bicycle tires on that car before you take it out on the road. The result is entirely predictable: A top-of-the-line vehicle that is now undrivable, one that might even need to be replaced if you chose to venture out.
Apply that installation methodology to the construction environment, and the result is the same.
Backed by the latest material science, today’s insulated metal panels (IMPs) offer durability and value as a building envelope solution. IMPs enable owners, architects and contractors to achieve their design vision with versatility – through color, texture and more. They also deliver desirable thermal performance at a time when building codes continue to raise the bar on energy efficiency.
What happens if those IMPs are not properly installed?
The results can range from minor irritations (an aesthetic issue) to costly and dangerous issues (total structural or thermal failure). In each case, such errors cost time and money.
Here are the top five installation mistakes with IMPs and how to avoid them on the construction site.
#1 – Assuming Every Application is the Same
These days, construction crews are likely accustomed to working with insulated metal panels as external cladding. In fact, they may have installed similar IMPs on another recent job.
Subcontractors sometimes assume that everything they do on any given installation should be the same based on certain installation practices they followed on another project.
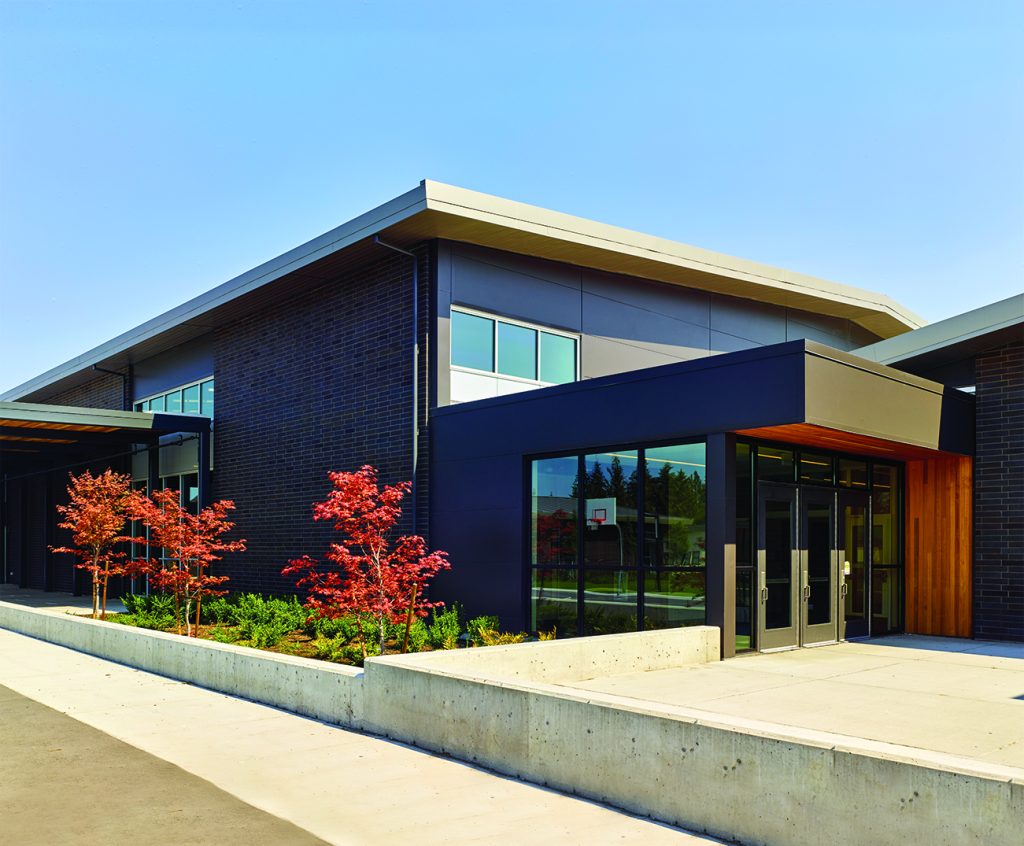
With IMPs, this is an oversight that can be costly.
Consider the vapor barrier, one of the critical functions of an IMP. It can be applied at the factory or on-site depending upon the panel. When installing panels for a cold storage environment, the “warm” side of the vapor barrier will always be on the exterior, whereas the vapor seal would be on the opposite side of the panel in a commercial/industrial application.
Get this reversed on the job site during installation, and you have a real problem.
#2 – Not Reading the Product Installation Guides
Product installation guides are often shipped with the materials to the job site. They are also readily available on the websites of the manufacturers.
Despite this, contractors often rely on their previous experience and assume they do not need to learn anything new. They figure they’ve been doing it properly all along.
They miss out on building their knowledge base and executing a clean installation of the project by not reading the guide, which might include additional details on how to receive and unload the panels and how to properly handle them.
#3 – Not Having the Proper Equipment
Let’s say a construction crew is anticipating the delivery of longer-length IMPs that are to be installed in a vertical orientation. Such a delivery might require two forklifts to unload and special lifting equipment to install the panels due to their length.
If only one forklift is available at the construction site, crews are not prepared to receive the delivery. Those same crews may end up damaging the product before it is installed, which requires replacement product to be manufactured and shipped. Again, this costs time and money and may delay the overall completion timeline for the building.
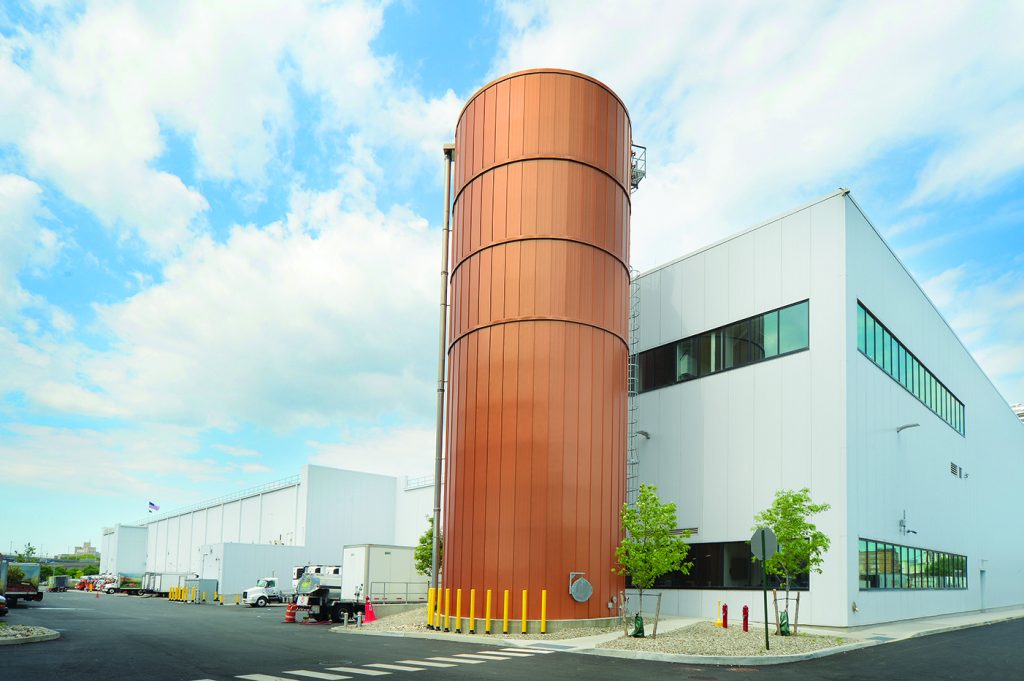
#4 – Framing Alignment and Tolerances
This is one of the most misunderstood and overlooked issues in the field when it comes to IMP installation.
The framing alignment is critical to a proper fit-up of the overall construction and to the panel’s efficiency and performance.
A framing misalignment can be the catalyst for a whole host of issues.
A crease or buckle on the face of a panel or a number of panels means those failing panels will need to be replaced.
If the misalignment is more systemic, it can lead to total structural failure of the panel system and require new product and a second installation of the system. This can lead to cost overruns, challenges with the building owner in terms of trust and a major interruption of the completion timeline.
#5 – Not Ordering Extra Panels
If a crew has only ordered enough panels to complete the job, they leave themselves vulnerable should any product get damaged – prior to its arrival, on-site, or during actual installation.
Loss of product due to damage means waiting for new panels to be manufactured. With panels that have special components, finishes, or colors, the lead time can be even longer, which means delaying the entire project.
Extra panels not installed on the job can be turned over to the owner of the building so they can be used to replace damaged panels during the life of the building.
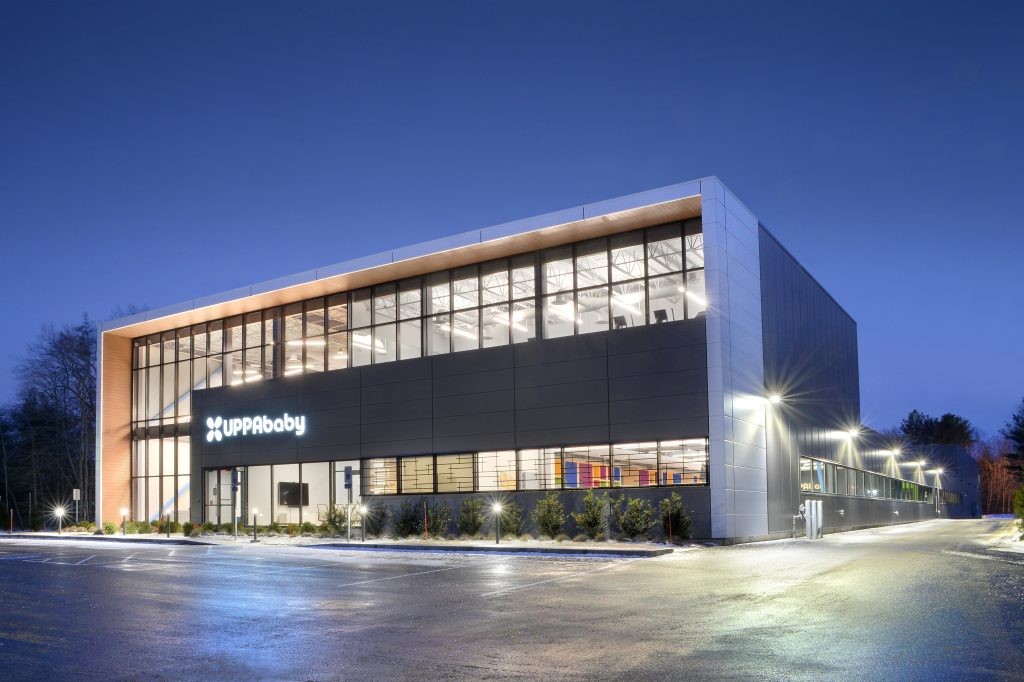
Get Proactive
The best advice for construction crews installing IMPs is to stay ahead of the curve:
- Know and understand the site conditions for the project. Is it prepared to receive materials? Are there conditions that might prevent the delivery of the product? What about conditions that might impact installation in general?
- Keep installation crews properly trained. What may have worked on a previous job may not be applicable to the new job.
- Review and consult installation guides and construction drawings, and when in doubt, consult with the manufacturer before beginning the installation process.
Have Questions About Our Products?
Please fill out the following information and an experienced sales representative will be in contact. We look forward to hearing from you!
View our Privacy Policy