In the quest toward reduced embodied carbon and renewable products, architects and specifiers are leaning into insulated metal panels (IMPs), which are made with recycled steel materials. The IMPs for walls are encapsulated by two steel facings with a foam core, which offers an advantage of thermal values and moisture protection in an integrated, all-in-one system. However, even though they have been on the market for decades, there are still some myths that architects and designers should be aware of, as well as tips for better, more durable building envelopes.
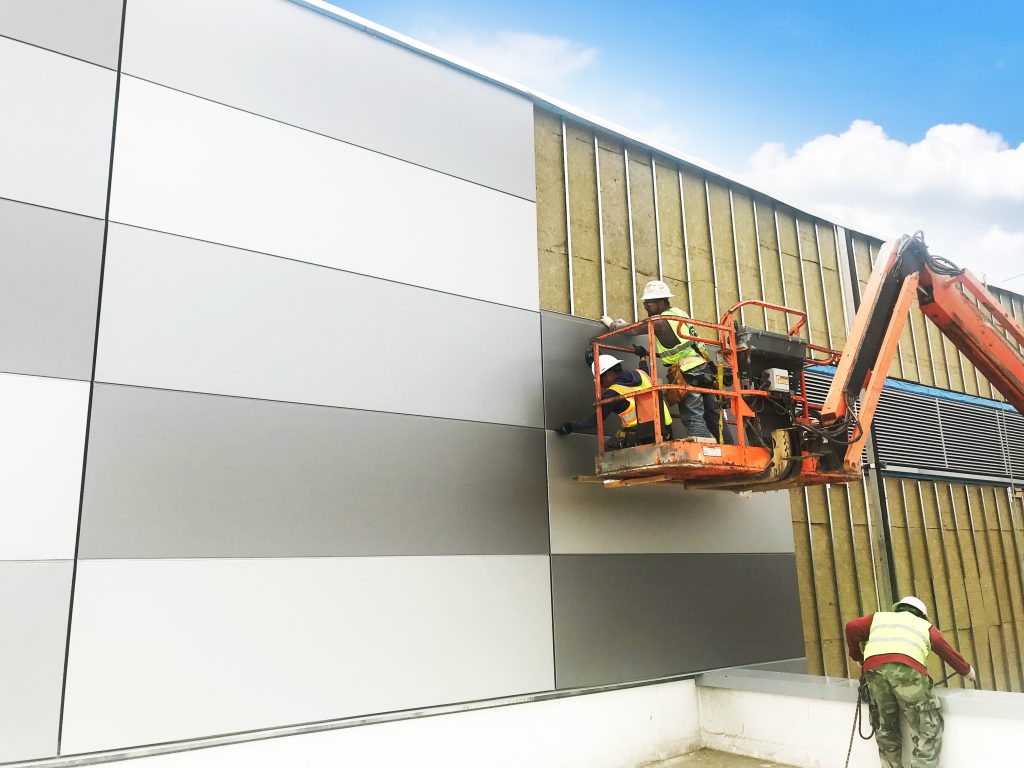
Myth 1: “All IMP Applications are Alike”
Some industry pros have a tendency to think all IMPs perform the same, regardless of color, profile, or length, and that is not the case. An important example is the design trend toward darker panels, including black panels. A caveat, however, is that the darker the panel is, the more thermal stress it takes on, especially with a design preference for flat panels, whereas other profiles would work better. If the panel color is too dark, thermal stress could start to compromise the performance of panels and cause aesthetic issues such as blisters and oil canning. Architects can balance that effect by designing with profile panels instead of flat panels. Another way to prevent issues is to always talk to manufacturers and ask them to do a thermal stress analysis, which can provide guidance on any risk factors.
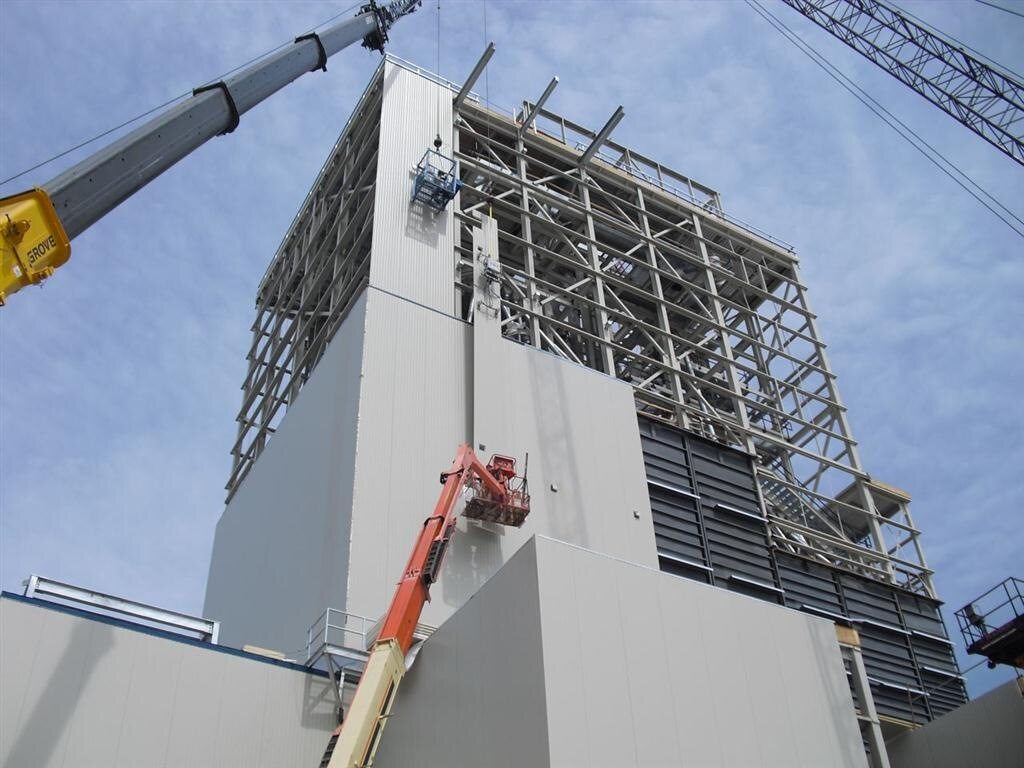
Myth 2: “It Can Be Fixed Later”
In today’s tight labor market, there is a need for more training, and placing high value on experienced installers. One of the biggest recurring installation mistakes is framing misalignment. It happens frequently due to untrained workers coming in, as well as retention issues. Quality installers are often overlooked due to the perception that their services are more expensive. However, when the costs of correcting errors made by untrained crew members are calculated, the expenses can become astronomically higher.
Designers should make sure they are choosing qualified, competent installers, fully versed in IMP installations. In some cases, hiring a full-time inspector makes sense, especially with massive projects of extremely high value. Thankfully, the Metal Building Contractors and Erectors Association (MBCEA) is leading the way with the AC478 standard, which focuses on the need for educating, training, and developing tools for its members and all industry professionals.
Myth 3: “On-site Verification is Difficult”
No matter the product quality or design, if panels are not correctly installed, leaks will occur. There is a simple verification that can be done on the jobsite using the AAMA 501.2 quality assurance and diagnostic field water check method to see if there are leaks. It is easy to do during installation and does not require a third-party technician; builders can do it themselves with a limited amount of equipment.
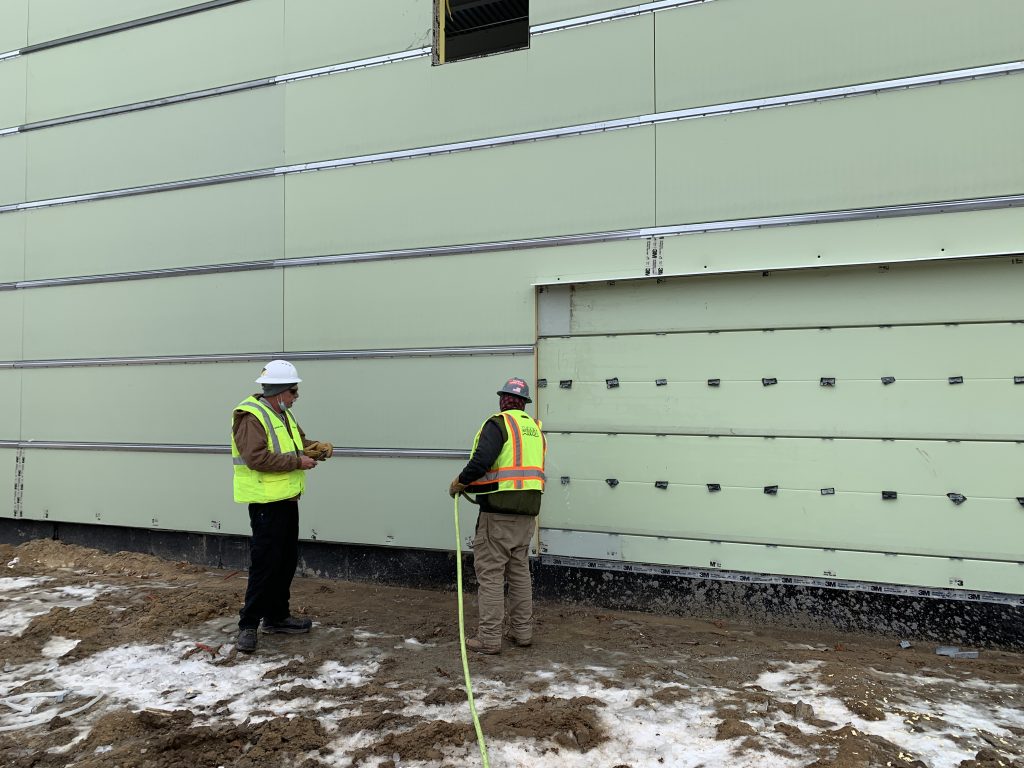
To complete the AAMA 501.2 test, installers use a 19 mm (0.75 in.) water hose and calibrated spray nozzle. When locating a water source is challenging, portable water tanks may be used to create pressure. Water is sprayed over an area to be tested at 0.3 m (1 ft) away for five minutes. The wall is then monitored for leaks. The process is done during installation, so any leaks found can be repaired prior to installing finishes. Catching leaks early and correcting them can avoid significant costs associated with future leak repairs.
Myth 4:”IMPs Cannot Be Used in Fire-Rated Walls”
Designers and builders should know there are multiple solutions in the panel market for fire-rated wall assemblies. They include IMPs with foam cores, not just single-skin panels used with masonry or mineral core panels. IMPs are manufactured with a Class 1 foam system. Class 1 foam systems do not burn until temperatures higher than 427 C (800 F) and self-extinguish when heat sources are removed. When IMPs are combined with gypsum sheathing, fire ratings of as long as three hours can be achieved. Mineral wool core panels are also available for fire-rated assemblies, but they do not have the same design flexibility as foam panels.
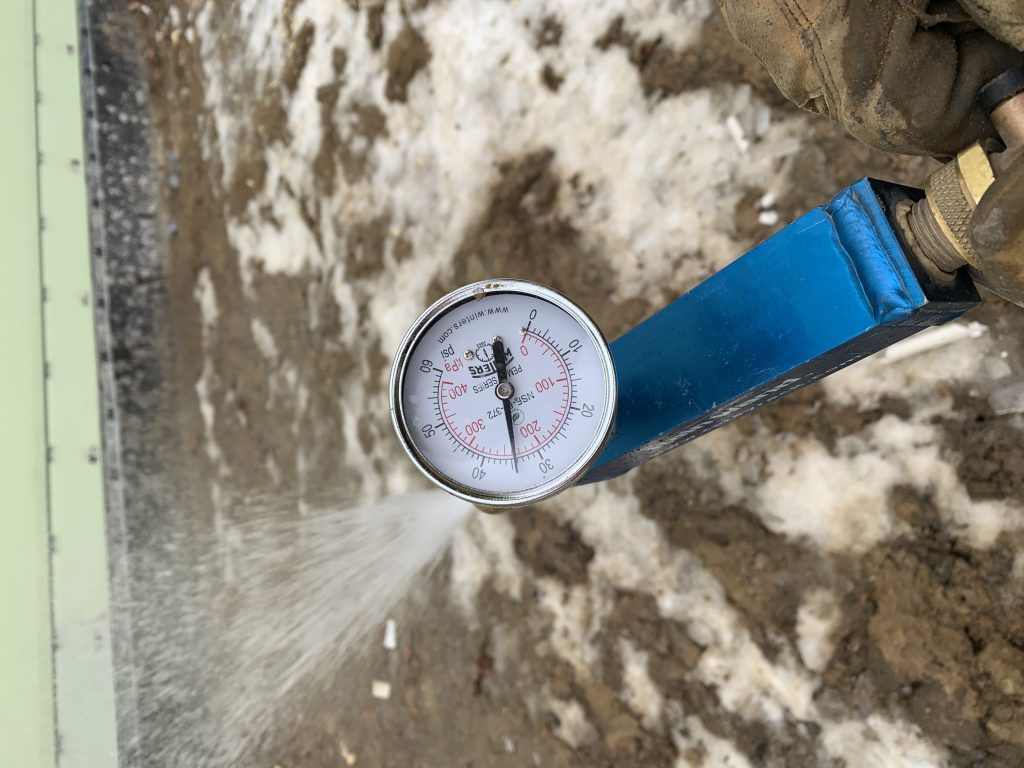
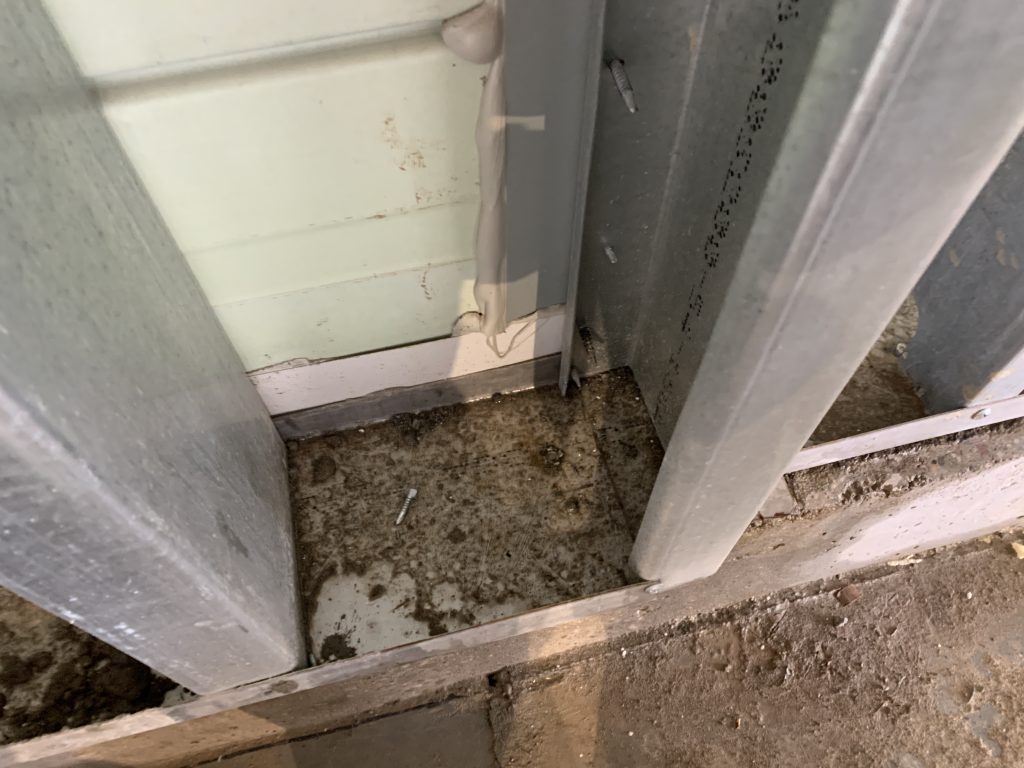
Myth 5: “The More Insulation and Barrier Layers, The Better”
The beauty of the IMP is that it provides an all-in-one solution of finish, insulation, and air and water barrier. Adding sheathing, water barriers, and additional insulation creates a risk of a double vapor barrier along with greater cost and complexity. Redundant layers do not necessarily mean better performance. With proper installation and best practices, IMPs can be the cost-saving solution for a variety of building envelope applications.
Arnold Corbin is the Technical Services Manager at Metl-Span, based in Lewisville, Texas. Corbin has more than 40 years of experience in the construction industry. His areas of expertise include project management, estimating, product and installation training, building envelope applications, building diagnostics, and product support.
Have Questions About Our Products?
Please fill out the following information and an experienced sales representative will be in contact. We look forward to hearing from you!
View our Privacy Policy